Product
Complete Turn-key solutions
Dry Mixture
- Parget offers technology for the production of gypsum based and cement based dry mixture.
- The key point of dry mixture production technology of Parget is flexible design based on the product formulation of the Customer, accurate dosing and weighing,constantly homogeneous mixing and accurate packing.
- Parget Dry Mixture Technologies provide the same homogeneity and product quality in every bag with perfect weight accuracy.
- Parget Dry Mixture Technologies includes additive feeding system, additive storage, automatic dosing and weighing system of main and chemical additives,
- mixing, and packing unit.
- Possibility of production of both type of products on one single line or two parallel lines.
Features | Benefits |
---|---|
Daily Capacity Final product range |
from 5 to 100 tons per hour. Possibility to produce different types od product according to different formulation. |
Dosing, Mixing and Packing Energy Consumption Plant Design |
Stable high accuracy. Very economical due to smart and optimal design of the plant. Flexible design of the plant based on Customer`s product formulation : Horizontal and vertical design of the plant |
Softwre Tchnical process Formulation |
Can be easily integrated with existing units Automatic control system based on Siemens SCADA and PLC with production reporting software High effectiveness and efficiency Provision of formulation according to the market needs |
Parget Dry Mixture Production Line Process
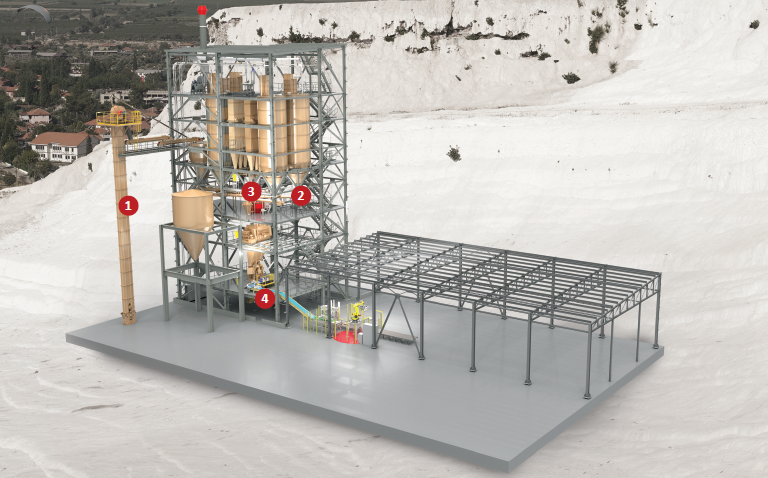
The process described below will be applied for the main additive feeding unit , main additive storage, dosing and weighing unit, chemical additive storage,weighing unit, mixing and packing unit. The quantity of storage silos and bins of main and chemical additives that will be used in the plant, depending on the type and range of the dry mixture. Based of the type of additive, different types of equipment can be used for feeding such as dens-conveyor, bucket elevator or direct feeding from bulk carrier.
The main additive storage unit consists of storage silos where the main additives will be stored and all other auxiliary equipment as silo top filter, fans etc.For each single additive will be used dosing equipment in order to dose and feed additives to weighing bin. Dosing and weighing machinery will be defined depending on the formulation of final product.
Chemical additive storage, dosing and weighing unit consist of the movable additive feeding system with dedusting filter, storage bins for each single additive,
micro dosing screw conveyors and micro weighing bins for stable high accuracy with possibility do weigh chemical additives till 75 grams for 1 ton of the product.After all main and chemical additives are dosed and weighed they fed to continiuos dry mixture for homogenius mixing . After mixing is completed, the mixed product will be fed to the packing bin automatically. Thanks to our years of experience and R&D, all procautions will be taken so that the additives will be mixed together homogeneusly without having problem with the quality.
After the packing of dry mixture in polipropilen or craft valve bags they are transfered to the next unit for manul or automatic palletsing and packaging. Other
alternative packing solutions are available as filling to big-bags, mobile silo or bulck carrier. Under the packing machinery we are using spiilage collectiong and feed back system in order no to have wastage.
Operation of the plant is automatic and continuous but based on batch method of production. Capacity desing of the plant is based on quantity of batch in one
hour from 10 to 12.Wide range of making formulation for final product and integrating them to the operation software. Thanks to the production reporting software, possibility to take information from software about all used additives and produced products basing on hourly, daily, monthly or yearly periods.
To reduce the production cost and shorten the pay back period of the invesments, Parget is taking in to consideration all the possible precautions which can
negativelly effect operation of the plant.
In order to arrange cost effective operation of the plant, capacity of dry mixture production plant is designed for maximum operation duration from 8 to 16 hours.Dry mixture plant designed in accordance with the capacity, formulation and range of the final products and it can be changed according to request of the Customer.
Parget Dry Mixture Factory’s Units
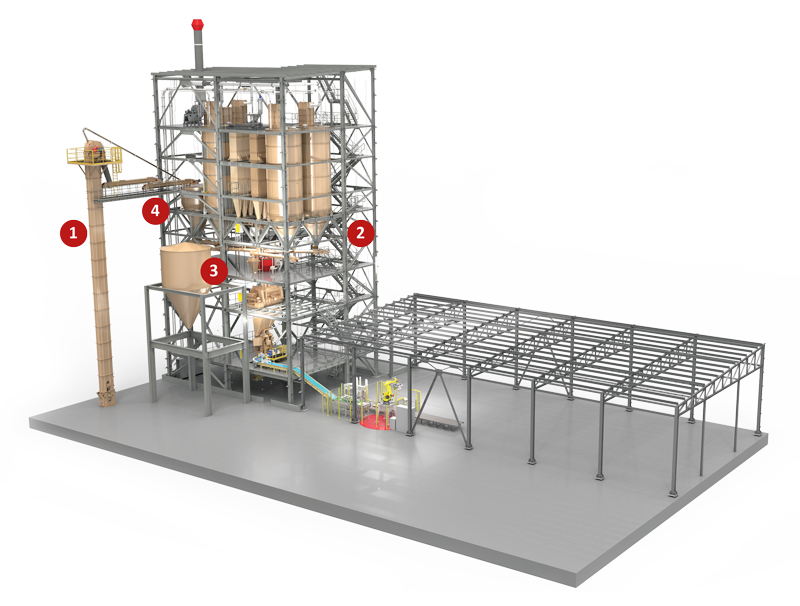
Main additive feeding and storage unit
- Properly choosen machinery and equipments based on the additive quantity, their fraction and method of their packaging and feeding to the dry mixture factory
- storage silos.
- Smart designed machinery and equipments for ease of maintenance
- Can be used different equipment as bucket elevator, pneumatic dens conveyors and feeding directly frombulk carriers
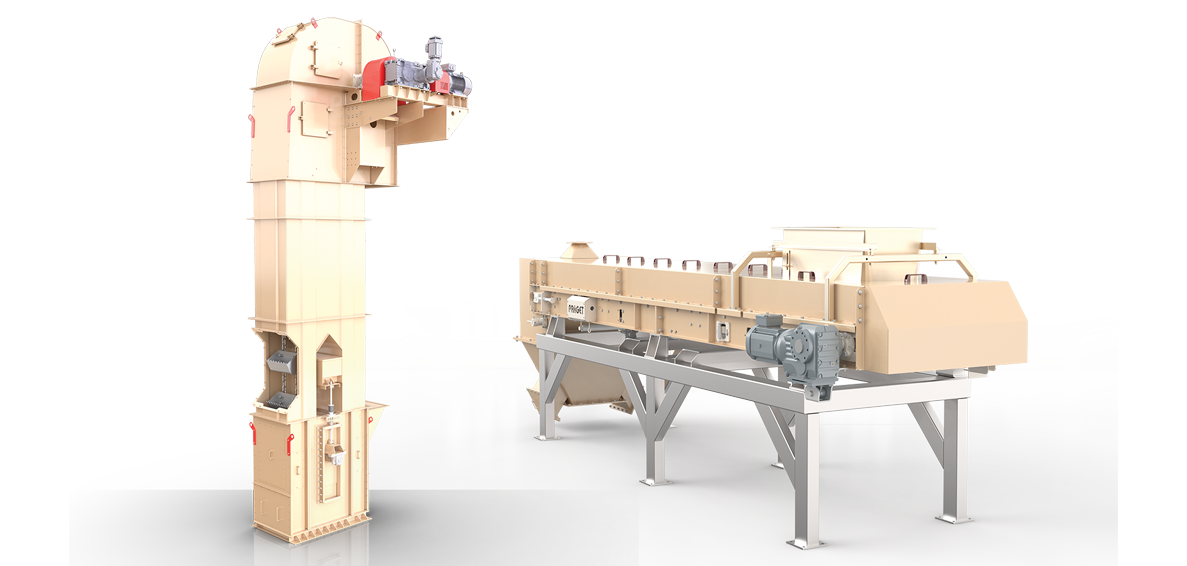
Dosing and weighing unit
- Automatic dosing and weighing
- Flexible design according to the quantity of additive used in the mixture.
- High accuracy and efficency dosing and weighing equipment
- Basing on additive type possibility of gravimetric and volumetric weighing
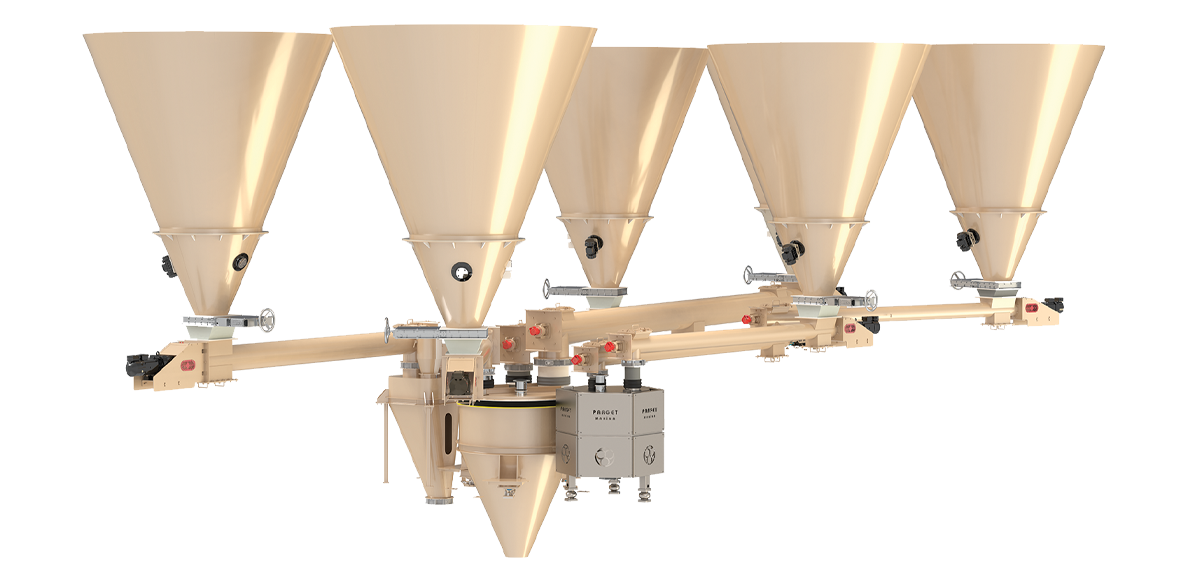
Mixing and packing unit
- Homogeneus and effective mixing
- Automatical and high accuracy packing
- Gain the spilled material back by the help of spillage collecting system
- Solutions for all possible request
- Automatic selection of product basing on the formulation uploaded to SCADA software.
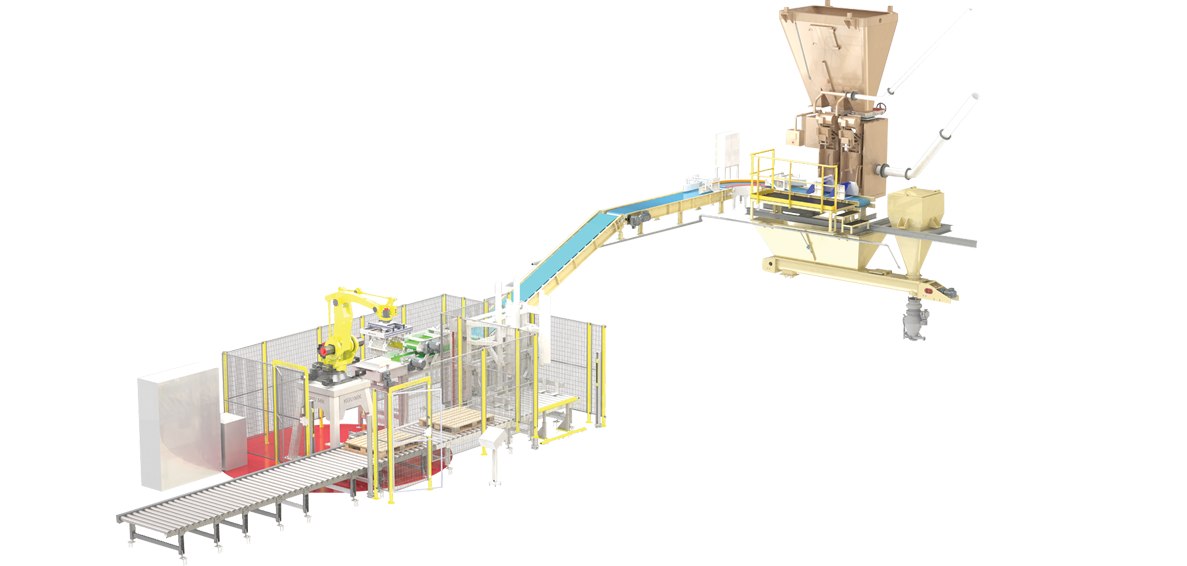
Chemical additive storage, dosing and weighing unit
- High accuracy and efficency dosing and weighing equipment.
- To extend the life time, properly choosen materials depending on the characteristic of the additive.
- Abillity to weigh till 75 gr per batch
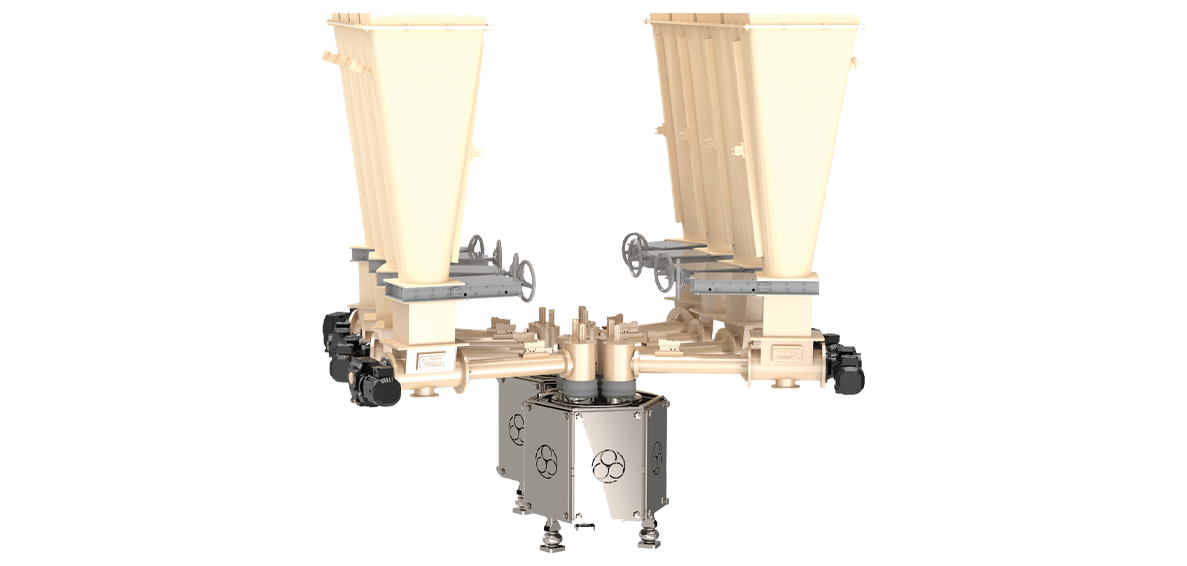