Machineries
Calcination, drying and cooling systems
1.Rotary kiln
Rotary calcination kiln is designed depending on required capacity and considering particle size and particle structure, Product type, particle size and feeding capacity define diameters.Length and inner construction of the kiln as well as filtration space. Gravitational flow and mechanical mixing enables movement of particles inside of the kiln, that ensures continuous change of contact area of a particles with heat. Thus, it enables high speed of calcination. Rotation speed of the kiln differs depending on characteristics of raw material and final material.
Steam, emitted during calcination, is relieved outside by means of cyclone and jet pulse filter due to vacuum affect. Material comes inside the kiln through the inlet placed on the upper part of cylindric body and comes out through outlet screen. Dilution chamber is the first place where hot air contacts with material. In order to keep heat inside, inner part is lined with refractory bricks). Inlet hood is installed between stationary dilution chamber and rotary kiln body. Connection place is sealed for heat insulation. Rotary kiln is a cylinder with a special inner longitudinal construction. It has four moving bearing houses and is installed on bearings in a certain angle. It rotates with a certain adjustable, normally, low speed by means of bull gear, pinion gear and rings. Rotary kılns are suitable for interrupted and uninterrupted processes. Due to special inner construction, material moves forward slowly and stays longer inside of the kiln. Thermocouples, placed at a certain interval along kiln body, enable control of inner temperature of kiln. Inlet helixes enable forwarding of material towards the kiln body without collection at the inlet. Outlet helixes, installed to the opposite direction of transportation, ensure collection of material at the outlet of the kiln and discharge it. Screen, coupled with the kiln, rotates together with the kiln and screens the material.
Machine Types | Burner Capacity | Machinery Capacity (t/day) |
---|---|---|
PM-RK1608 | 2 MW | 100 - 120 |
PM-RK2012 | 2.5 MW | 120 - 150 |
PM-RK2214 | 3.5 MW | 200 - 240 |
PM-RK2417 | c | 240 - 300 |
PM-RK2618 | 6 MW | 350 - 420 |
PM-RK2820 | 8 MW | 500 - 550 |
PM-RK2820 | 10 MW | 600 - 700 |
PM-RK3022 | 12 MW | 750 - 900 |
PM-RK3224 | 15 MW | 900 - 1200 |
Rotary Kiln Advantages
- Stable feeding to the kiln
- Continuous rotary kiln with special inner design;
- Easily operated
- Have high controllability,
- Acquiring calcined gypsum with correct, required characteristics
- Achieving higher capacity with signle unit
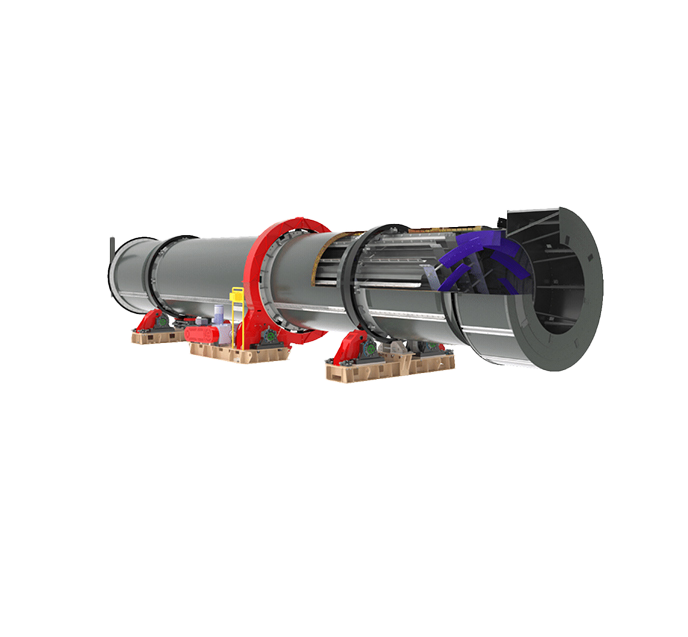
2.Vertical kiln
With the vertical kiln process; calcination takes place slowly under high pressure and in direct contact with hot air. Thanks to this slow and pressured calcination; high quality plaster obtained has similar characteristics to a mixture of 85% hemihydrate and 15% alpha-hemihydrate.
This type of kiln is static type and the plaster moves by gravity. The raw gypsum feeds into the kiln via screw conveyor from weighing silo and gypsum fed from top into the center of the kiln. The combustion chamber is in the center and manufacturing material is 1.4301 and 1.4845 quality stainless steel. Burner placed at the top of the kiln produces hot gases flowing through the gypsum, descending from bottom to top, ensuring the rotational movement and, therefore, the uniformity of the calcination.
Product And Gas Flow Descrition
As shown in next picture; the raw gypsum is feed into the kiln from the center of the kiln via screw conveyor. These raw gypsums are going down vis gravity from the surface of the combustion chamber and while pile up on the each section of the chambers; the hot gas which comes from the combustion system come into contact with raw gypsum. During this time; the calcination occurs.
The rising hot gas are collection into the dedusting filter which are connected directly on top of the kiln. The kiln has the pressure inside and to the this pressure and gas / dust from the system; the kiln has a dedusting filter on top pf the kiln. This filter will be jet pulse cleaning system and with proper type of bags. And the emission of the value from chimney will be like below:
The vertical kiln is also equipped with loadcells to measure the final product. Besides; the kiln will be equipped with temperature sensors and pressure sensors to arrange the calcination parameters.
Tempretaure sensors will be totally 6 pcs; 4 is in the side of the kiln with 0-300 °C and 1 is in the filter bags and 1 is in the combustion chamber. Besdies, will be used a pressure switch in the piping from blower to set a pressure ( 0-1 bar)
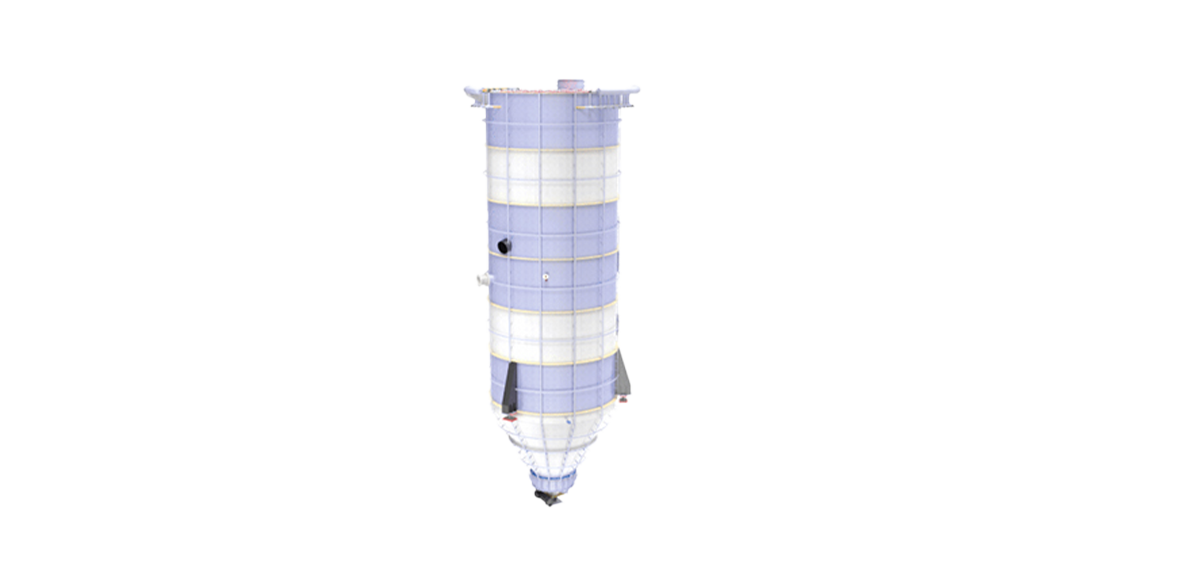