A PHP Error was encountered
Severity: Warning
Message: Undefined variable $kategori
Filename: urunler/detay.php
Line Number: 39
Backtrace:
File: /var/www/vhosts/parget.com.tr/httpdocs/sites/other/pargetmakina/views/urunler/detay.php
Line: 39
Function: _error_handler
File: /var/www/vhosts/parget.com.tr/httpdocs/application/libraries/Template.php
Line: 550
Function: view
File: /var/www/vhosts/parget.com.tr/httpdocs/application/libraries/Template.php
Line: 517
Function: _load_view
File: /var/www/vhosts/parget.com.tr/httpdocs/application/libraries/Template.php
Line: 186
Function: _find_view
File: /var/www/vhosts/parget.com.tr/httpdocs/modules/base/controllers/BasePublicController.php
Line: 56
Function: build
File: /var/www/vhosts/parget.com.tr/httpdocs/sites/other/pargetmakina/controllers/Contents.php
Line: 171
Function: buildForm
File: /var/www/vhosts/parget.com.tr/httpdocs/index.php
Line: 13
Function: require_once
A PHP Error was encountered
Severity: Warning
Message: Trying to access array offset on value of type null
Filename: urunler/detay.php
Line Number: 39
Backtrace:
File: /var/www/vhosts/parget.com.tr/httpdocs/sites/other/pargetmakina/views/urunler/detay.php
Line: 39
Function: _error_handler
File: /var/www/vhosts/parget.com.tr/httpdocs/application/libraries/Template.php
Line: 550
Function: view
File: /var/www/vhosts/parget.com.tr/httpdocs/application/libraries/Template.php
Line: 517
Function: _load_view
File: /var/www/vhosts/parget.com.tr/httpdocs/application/libraries/Template.php
Line: 186
Function: _find_view
File: /var/www/vhosts/parget.com.tr/httpdocs/modules/base/controllers/BasePublicController.php
Line: 56
Function: build
File: /var/www/vhosts/parget.com.tr/httpdocs/sites/other/pargetmakina/controllers/Contents.php
Line: 171
Function: buildForm
File: /var/www/vhosts/parget.com.tr/httpdocs/index.php
Line: 13
Function: require_once
Alçı
A PHP Error was encountered
Severity: Warning
Message: Undefined variable $kategori
Filename: urunler/detay.php
Line Number: 39
Backtrace:
File: /var/www/vhosts/parget.com.tr/httpdocs/sites/other/pargetmakina/views/urunler/detay.php
Line: 39
Function: _error_handler
File: /var/www/vhosts/parget.com.tr/httpdocs/application/libraries/Template.php
Line: 550
Function: view
File: /var/www/vhosts/parget.com.tr/httpdocs/application/libraries/Template.php
Line: 517
Function: _load_view
File: /var/www/vhosts/parget.com.tr/httpdocs/application/libraries/Template.php
Line: 186
Function: _find_view
File: /var/www/vhosts/parget.com.tr/httpdocs/modules/base/controllers/BasePublicController.php
Line: 56
Function: build
File: /var/www/vhosts/parget.com.tr/httpdocs/sites/other/pargetmakina/controllers/Contents.php
Line: 171
Function: buildForm
File: /var/www/vhosts/parget.com.tr/httpdocs/index.php
Line: 13
Function: require_once
A PHP Error was encountered
Severity: Warning
Message: Trying to access array offset on value of type null
Filename: urunler/detay.php
Line Number: 39
Backtrace:
File: /var/www/vhosts/parget.com.tr/httpdocs/sites/other/pargetmakina/views/urunler/detay.php
Line: 39
Function: _error_handler
File: /var/www/vhosts/parget.com.tr/httpdocs/application/libraries/Template.php
Line: 550
Function: view
File: /var/www/vhosts/parget.com.tr/httpdocs/application/libraries/Template.php
Line: 517
Function: _load_view
File: /var/www/vhosts/parget.com.tr/httpdocs/application/libraries/Template.php
Line: 186
Function: _find_view
File: /var/www/vhosts/parget.com.tr/httpdocs/modules/base/controllers/BasePublicController.php
Line: 56
Function: build
File: /var/www/vhosts/parget.com.tr/httpdocs/sites/other/pargetmakina/controllers/Contents.php
Line: 171
Function: buildForm
File: /var/www/vhosts/parget.com.tr/httpdocs/index.php
Line: 13
Function: require_once
Parget Alçı Teknolojileri en uygun tasarım ve en iyi çözümleri sunarak, optimal kalitede alçı tozu elde etme imkanı sunmaktadır
Müşteri odaklı yaklaşımı, deneyimli proje yönetimi ekibi ve etkili satış sonrası hizmetleri sayesinde Parget Makina, müşterilerinin ihtiyaçlarını anlayan güvenilir bir çözüm ortağı olarak sektörde yer almaktadır.
Özellikler | Faydalar |
---|---|
Günlük Kapasite |
Esneklik: Günlük 100 ila 1000 ton arası üretime sahip farklı kapasitelerde tesisler sunulmaktadır. |
Nihai Ürün Yelpazesi | 0-160, 0-200, 0-400, 0-630, 0-1000 μ ve diğer fraksiyonlar gibi farklı tane boyutlarında nihai ürün elde edilebilmektedir. Nihai ürün tane dağılımını kontrol edebilme imkanı verilmektedir. 5 dakikadan, 30 dakikaya kadar değişkenlik gösteren donma sürelerinde nihai ürün elde edilebilmektedir. |
Kalsinasyon Süreci | Kullanım alanına uygun, doğru, istikrarlı ve gereken özelliklere sahip nihai ürün elde edilebilmektedir. |
Enerji Tüketimi | Isı geri kazanım sistemleri ve optimal çalışma süreleri sayesinde son derece ekonomik ve çevre dostu bir tesis sunulmaktadır. Doğalgaz, HFO ve dizel gibi farklı yakıtlarla üretim yapabilme imkanı sağlanmaktadır |
Tesis Tasarımı | Prosesle ilgili bir çok esnekliğin yer aldığı, kullanıcı dostu bir üretim fırsatı sunulmaktadır. Döner fırın, dikey fırın gibi her türlü prosese uygun, farklı alternatifler, beraberinde getirdiği tüm avantajlarla müşteriye sunulmaktadır.Müşteri ihtiyaçlarına uygun tasarım. |
Elektrik ve otomasyon | Kontrol edilebilir, güvenli ve kullanımı son derece kolay bir elektrik otomasyon sistemi sağlanmaktadır. Tamamen otomatik kontrol sistemi sayesinde insan hatası minimize edilerek, istenilen kaliteye ulaşma hedefi daha kolay yakalanmaktadır. Minimum insan ihtiyacı sayesinde üretim maliyetleri en aza indirilmektedir. |
Teknik süreç | Yüksek etkinlik ve verimlilikli makinalar sayesinde kaliteden ödün vermeksizin, maksimum üretim sağlanmaktadır. Firesiz üretim sayesinde üretim maliyetleri düşürülmekte ve kullanıcıya pazarda rekabet gücü sağlanmaktadır. |
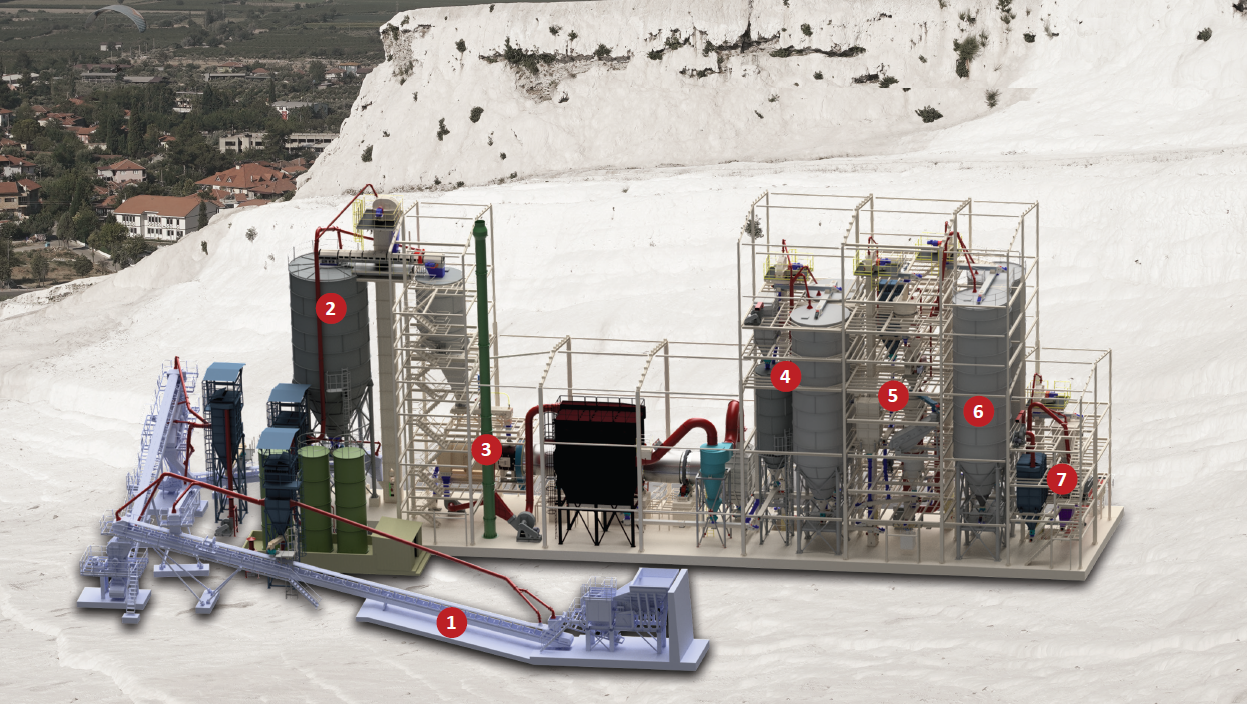
Aşağıda; ince ve kaba alçı tozu üretimi için tasarlanmış olan tesislerin nasıl çalıştığı anlatılmaktadır. Alçı tozu üretim tesisi; kırma-eleme, hammadde depolama ve besleme, kalsinasyon, öğütme-sınıflandırma-eleme, nihai ürün depolama ve paketleme ünitelerinden oluşmaktadır.
Alçı taşı; kırma ve eleme ünitesinde yer alan besleme bunkerinden sisteme beslenmektedir. Kırıcının önüne konumlandırılmış olan manyetik separatör sayesinde hammaddenin içinde yer alan metal parçaların, kırıcıya ve dolayısıyla girmesi engellemekte ve bu sayede kırıcı veya sistemde ortaya çıkacak olası sorunlar giderilmektedir. İstenilen tane boyutunu elde etmek amacıyla kırıcılar sayesinde kırılan alçı taşı, vibrasyonlu kontrol eleğinden geçerilir ve sisteme beslenmesi gereken 0-10 mm boyutundaki hammadde, daha büyük tanelerden ayrıştırılır. Daha büyük taneler bant konveyör vasıtasıyla yeniden kırılmak üzere sisteme geri beslenirken, ihtiyaç duyulan malzeme de sisteme beslenmiş olur. Kırma ve eleme ünitesi yer alan tozsuzlaştırma sistemleri sayesinde, proses esnasında oluşan toz sistemden uzaklaştırılarak hem tozsuz bir ortam sağlanmakta hem de tozun sisteme geri beslenmesi sayesinde fire ortadan kaldırılmaktadır.Sistemde kullanılan frekans konvertörü ile donatılmış dozajlama makinaları sayesinde; makinaların birbiriyle koordine çalışabilmesine imkan verilmektedir.
Kırma ve eleme ünitesinde elde edilen 0-10 mm hammadde, hammadde stoklama ve besleme ünitesinde depolanmaktadır. Bu sayede kırma eleme sistemi; istenildiğinde ihtiyaç duyulan hammadde kapasitesinin üzerinde çalıştırılır ve istenildiği zaman, üretime etki etmeksizin durdurulabilmektedir. Aynı zamanda kırma eleme ünitesinde olası bir bakım veya tamir işlemi esnasında sistem durdurulmaksızın, hammadde stoklama ve besleme ünitesindeki silolardan sisteme beslenebilmektedir. Stok siloları tamamen dolu olduğunda, operatör müdehalesine gerek duymaksızın sistem otomatik olarak, kendi kendini durdurabilmektedir. Sistem öncelikli olan fırın besleme silosunu doldurmayı hedeflemektedir.
Fırın besleme silosu içerisindeki malzeme, maksimum seviye sensörü hizasına ulaştığında, sistem otomatik olarak hammadde stok silosuna malzemeye doldurmaya başlamaktadır. Tüm silolar dolduğunda ise makinalar sıralı olarak durmaktadır.Hammadde stoklama ve besleme ünitesinden; sisteme beslemeye elverişli hammadde, dengeli ve üretim yapılan kapasiteye uygun şekilde tartılıp, dozajlanarak döner kalsinasyon fırınına beslenir. Bu sürece tartımlı bantlı konveyör aracılık etmektedir. Hammadde düzenli ve kesintisiz olarak döner kalsinasyon fırınına beslenir. Döner kalsinasyon fırını beslenen malzemenin homojen bir şekilde kalsine edilmesini sağlamaktadır. Kalsinasyon; hammaddeye, üretilecek olan nihai ürünün parametrelerine uygun ısıyı vermek suretiyle, hammaddenin içerdiği suyun bir kısmının buharlaştırılması esasına dayanmaktadır.Kalsinasyon bir kimyasal reaksiyon olup, hammaddenin ısıyla buluştuğu anda başlayıp, belli sıcaklığa kadar düşene kadar devam etmektedir. Bu sebeple döner kalsinasyon fırınından çıkan alçı tozunun, direk olarak öğütülmesi, istenilen kalite parametrelerinden feragat edilmesine sebep olabilir. Döner kalsinasyon fırınından çıkarılan alçı tozunun sıcaklığının düşürülmesi suretiyle daha stabil bir kalitenin yakalanması hedeflenmektedir.
Bu amaca uygun; alçı tozu ara stoklama ve normalizasyon ünitesindeki silolarda bekletilmektedir. Alçı tozunun sıcaklığının düşürüldükten sonra öğütülmesi sayesinde, ardışık ünitelerdeki makinaların dayanım ömürleri uzatılmakta, olası bakım faaliyetleri için kalsinasyon ünitesini durdurma ihtiyacı güdülmeksizin zaman kazanılmaktadır. Kalsine edilmiş alçı daha sonra aktarma makinaları vasıtasıyla; öğütme, sınıflandırma ve eleme ünitesine taşınmaktadır. Bu ünitede alçı tozu; değirmende öğütüldükten sonra talep edilen nihai ürün fiziksel parametrelerine uygun şekilde seçilen makinalarda işlenmektedir. Kaba alçı tozu (0-1000 μ) üretimi amaçlandığında öğütülen alçı tozu titreşimli elek vasıtasıyla elenerek istenilen tane boyutu sistemden alınmakta, daha büyük taneler ise yeniden öğütülmek üzere sisteme geri beslenmektedir. Kullanılan titreşimli eleğin, elek telini değiştirmek suretiyle farklı tane boyutlarında üretim yapılması da mümkün kılınmaktadır. İnce alçı tozu (0-200 μ) üretimi için ise; öğütülen alçı tozu dinamik havalı separatöre beslenerek, istenile tane boyutundaki alçı tozu sistemden ayrıştırılmakta ve istenilmeyen ürün, yeniden öğütülmek üzere sisteme geri beslenmektedir.
Farklı tane boyutlarındaki alçı tozu daha sonra paketlenmeden önce stoklanacakları; stoklama ünitesindeki silolara, tane boyutlarına göre doldurulmaktadır. Stoklanan nihai ürün paketleme ünitesine aktarılır ve paketleme ünitesinde 15 kg ila 50 kg arası istenilen torba ağırlığına uygun bir şekilde paketlenir. Paketleme makinaları hem kraft tip hem de PP torbaları paketleme opsiyonuna sahiptir. Tesis kapasitesi ve talep edilen paketleme hızına bağlı olarak; paketleme makinaları lineer tip veya döner paketleme makineleri ile tasarlanabilmektedir. Bu makinelerde otomatik olarak tartılırak, doldurulan torbalar, torba düşürme bandına düşürülmektedir. Akabinde talep edildiği şekilde; ister manuel olarak elle, ister paletleme makinaları yardımıyla paletleme yapılabilmekte ve yine ister manuel olarak elle, ister otomatik streçleme makinalarıyla streçlenebilmektedir. Paketlenen alçı tozu talep edildiğinde paletleme yapılmaksızın, kamyon yükleme bantları sayesinde doğrudan kamyonlara yüklenebilmektedir. Parget Makina bu konuda da müşteri talebine göre pek çok farklı opsiyon sunmakta ve hız, ekonomi, süreklilik gibi pek çok faktörü sorun yaşamaksızın müşterilerine sunmaktadır.Parget Makina’nın fireye olanak tanımaksızın üretim anlayışı gereği; esnasında çıkan toz, toz toplama bunkerlerinde, tozsuzlaştırma sistemlerinde tutularak sisteme geri beslenmektedir. bu sayede hem üretim maliyetlerinin düşürülmesi hem de çalışanlar için daha sağlıklı ve çevre dostu bir üretim hattı oluşturmak hedeflenmektedir.
Parget Alçı Tesisi Üniteleri
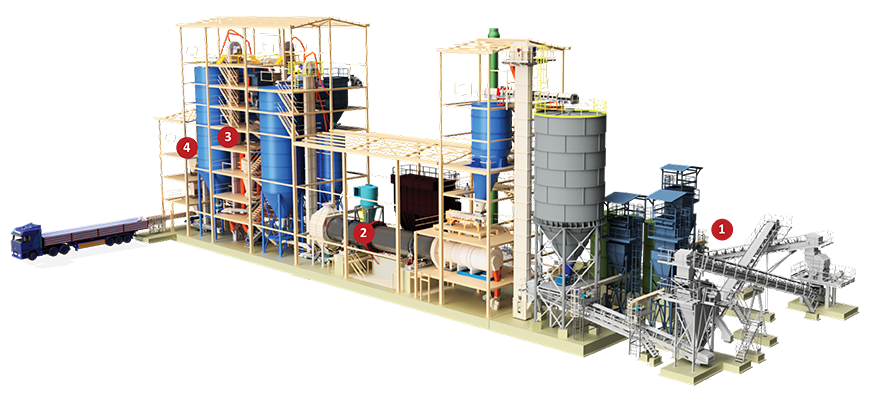
Kırma ve Eleme Ünitesi
- Kırma ve Eleme Ünitesi, hammadde giriş boyutuna, tesisin kapasitesi ve hammaddenin sahip olduğu fiziksel ve kimyasal özellik ve şartlara uygun tasarlanmaktadır. Bu kriterlere göre ünitedeki makinaların tipleri ve boyutları belirlenmektedir.
- Ünitenin temel kullanım amacı; kalsinasyon sisteminin ihtiyaç duyduğu 0-10 mm tane boyutundaki hammaddeyi hazırlamaktır.
- Üretim maliyetlerini en aza indirip, işçi sağlığını gözetlerken aynı zamanda tesisin de kesintisiz çalışması amaçlanmakta ve kırma eleme üniteleri günde 8 ila 16 saat çalışacak şekilde tasarlanmaktadır.
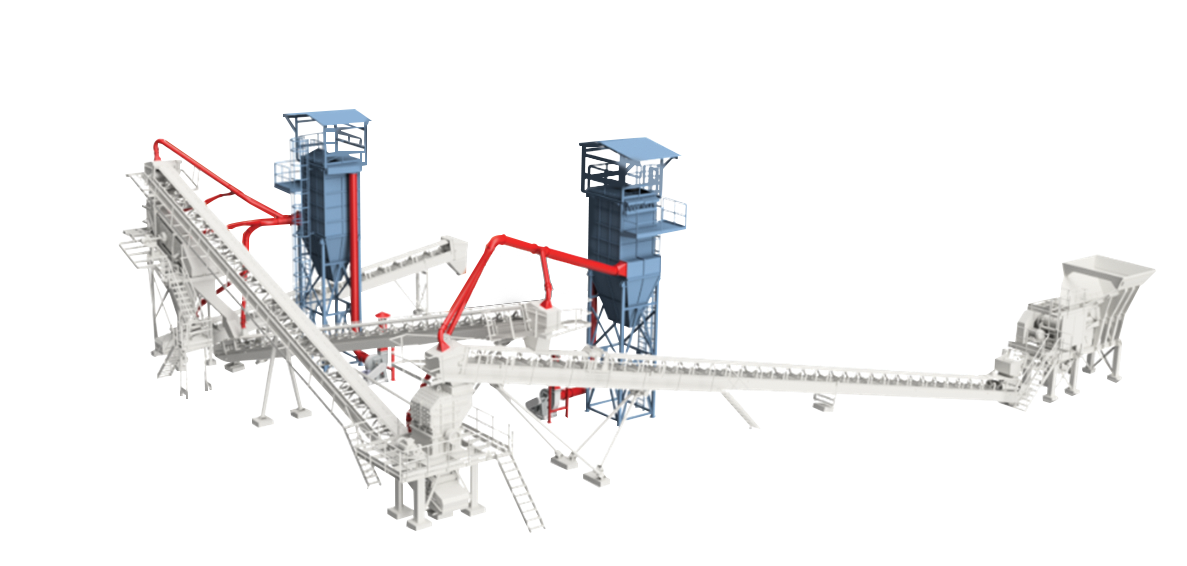
Kalsinasyon Ünitesi
- Parget Makina kalsinasyon sistemleri; firmanın sektördeki uzun yıllar boyu edindiği tecrübe ve bilgi sonucu geliştirmiş olduğu akılcıl çözümler sayesinde; hammadde ile alevin doğrudan temasını engelleyerek daha yüksek kalitede ürün elde edilmesini sağlamaktadır. Bunun amaçla döner kalsinasyon fırınları ile brülör arasında, fırın boyutlarına uygun olarak tasarlanmış yanma odası ve dilotasyon odası kullanılmaktadır.
- Kalsinasyon sistemi, enerji geri kazanım sistemi barındırmaktadır. Frekans konvertörü ile çalıştırılan sekonder fan vasıtasıyla, baca gazı sisteme geri beslenmektedir. Bu sayede hem gerekli ısıl enerji ihtiyacı düşürülmekte hem de baca gazının içerdiği alçı buharı sisteme geri beslenerek daha mukavemetli ve kaliteli alçı tozu üretilmektedir.
- Bu ünitedeki tartımlı bantlı konveyör, döner kalsinasyon fırın, kalsinasyon ünitesi filtresi fanı ve sekonder fan frekans konvertörleri ile donatılmaktadır. Bu sayede; bir çok parametreyi aynı anda kontrol etme fırsatı sağlanarak gerek kullanıcılara büyük esneklikler gerekse geniş ürün yelpazesi üretim yapma olanağı sağlanılır.
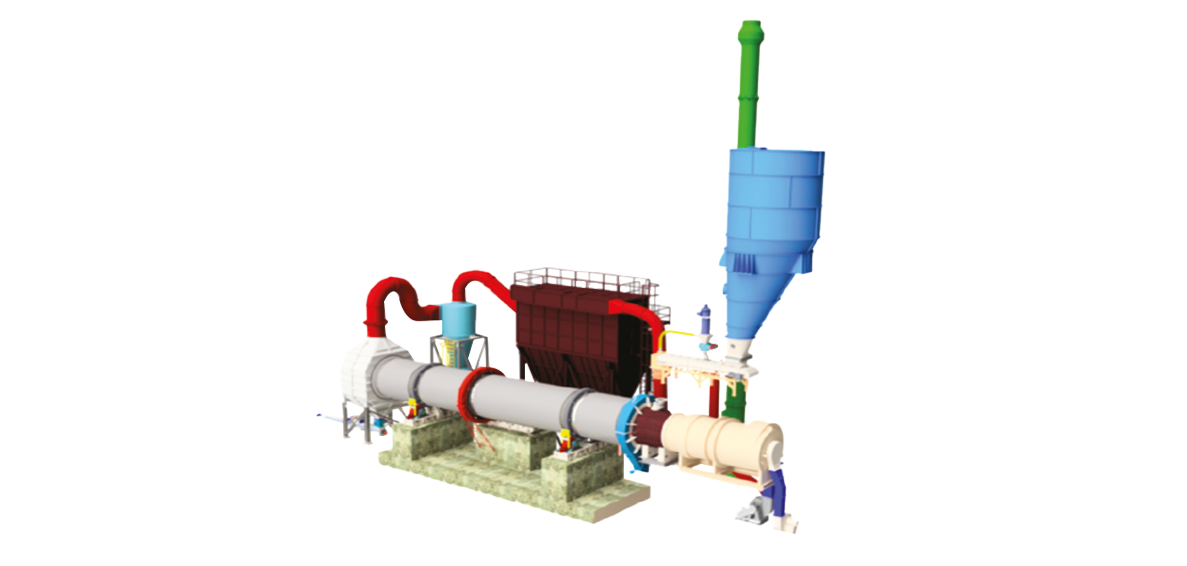
Öğütme, sınıflandırma ve eleme ünitesi
- Öğütme, sınıflandırma ve eleme ünitesinde 0-100 mikrondan 0-1250 mikrona kadar geniş bir yelpazede nihai ürün üretebilecek şekilde tasarlanmıştır.
- Sisteme entegre tozsuzlaştırma sistemleri ile tozdan arındırılmış bir çalışma ortamı, firesiz üretim ve düşük üretim maliyetleri sağlanmaktadır.
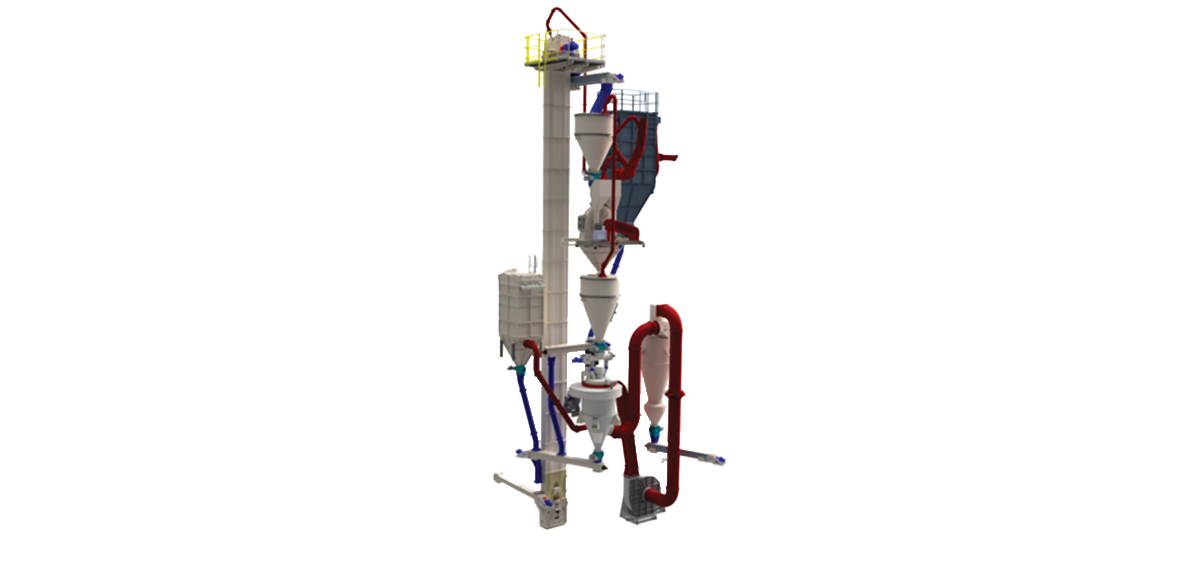
- İşçilik giderlerini dolayısıyla da üretim maliyetlerini azaltmak amacıyla paketleme üniteleri günde 12-16 saat çalışacak şekilde boyutlandırılmaktadır.
- Tesisin kapasitesine bağlı olarak, bu ünite lineer veya döner paketleme makineleri ile donatılabilmektedir.
- Torbaların tartılıp, doldurulması tamamen otomatik olup, istenildiğinde torbaların makinaya beslenmesi de otomatik olarak yapılabilmektedir.
- Paketleme ünitesi, süreç esnasında ortaya çıkan tozu tutup geri besleyen sistemlerle donatılmıştır.
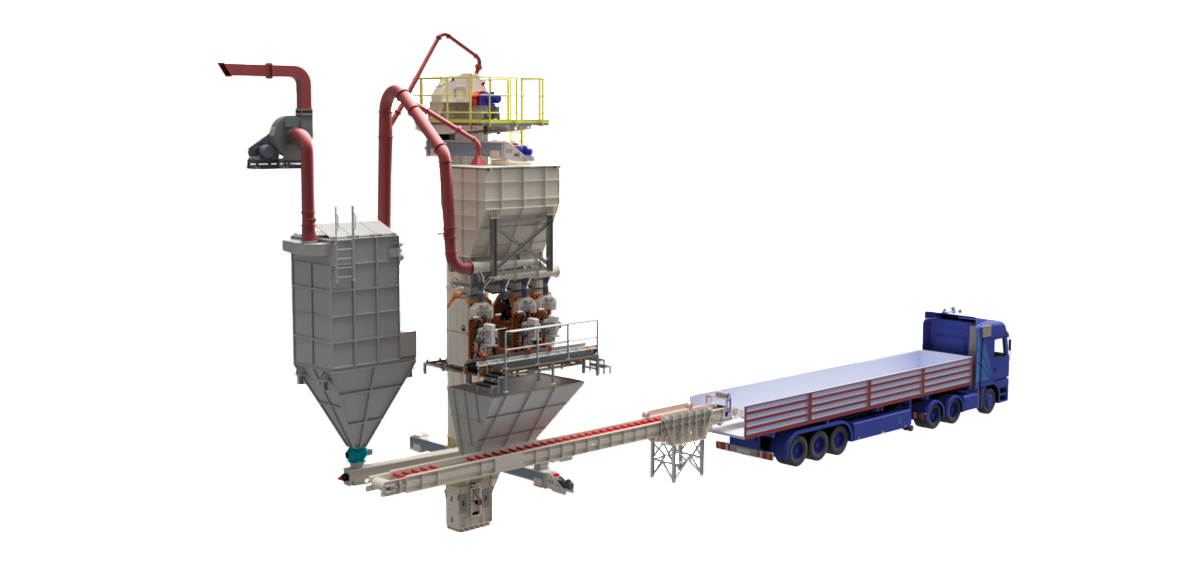