Product
Complete Turn-key solutions
Lime
Lime Production
In cooperation with the biggest lime kiln and hydrator technology supplier Maerz Ofenbau, Parget Makina designs and supplies complete turn-key plants for calcined, grinded and hydrated lime production, to ensure that the products meet market requirements and comply with customer specifications.
The main advantage of purchasing lime technology from Parget with Maerz Ofenbau cooperation is to receive coordination, project managment and intergration of different units of Lime plant by one single company Parget Makina which will simplify and reduce project risk of the Customer.
Features | Benefits |
---|---|
Daily Capacit Calcination process Final product |
Flexibility : from 150 to 1000 tons per day With Vertical kiln designed by Maerz Calcined lime Grinded lime |
Energy Consumption Plant Design |
Hydrated lime Possibility to use different fuels as natural gas, heavy fuel oil, diesel, coal etc Very economical and environmental friendly Flexible layout according to customer needs |
Complete automation Technical process |
Controllable, secure and easy in use process Low operation cost due to low number of staff involved. High effectiveness and efficiency Easy and practical project coordination and management due to Parget&Maerz cooperation |
No production waste |
Parget Lime Production Line Process Description
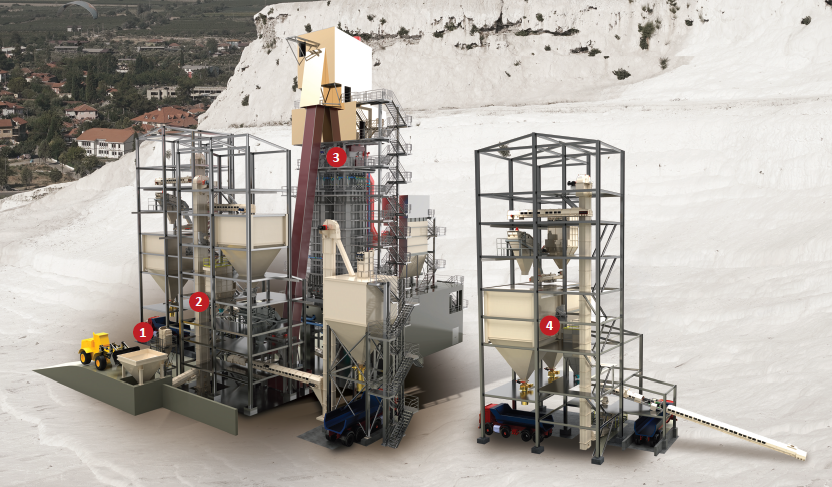
The process described below will be applied for the Raw material feeding, storage and screening, calcination , crushing and storage unit, hydration.
Raw material feeding , storage and screening unit is used to feed, store and control screening of raw material and feed it to the vertical kiln. Raw material with a fraction 40-80 mm is fed from feeding equipment to storage silos with belt conveyors. Instead of using long tranfer belt conveyor, it is also possible to use bucket elevator conveyor. Dedusting of the unit will be done by the dedusting filter and fans.
The raw material storage and the screening unit mainly consist of the storage silo where the raw material is stored, the vibratory screen to screen and prepare the raw material according to the tolerances. Even if the material is brought with requested fractions, it may be crushed during transfer and storage. Therefore, it must be screened again, brought into requested tolerances, and then fed to the calcination unit.
The calcination unit consists of the kiln, weighing and charging equipments, the vertical lime calcination kiln and the dedusting system. The prepared material will be weighed and fed to the skip bridge bucket and later with skipper winch it will be transfered to the calcination kiln. Depending on the final product, the raw material will be calcined under a certain temperature, pressure and time inside the kiln and later discharged by the help of the kiln discharging equipment to the discharge to belt conveyor. Meanwhile the necessary dedusting will be provided by the kiln dedusting system filter. The inside of vertical kiln is lined with different refractory materials. All air flow of the kiln is done and automaticly controled by traps, blowers and hydraulic system.
The calcined lime will be discharged to the belt conveyor to be transferred to the lime handling, storage, crushing and filling unit. This unit is used to produce the calcined lime according to the final usage of the product. Particle size and their range will be specified by the Customer. The lime will be fed from the kiln to the crusher to be crushed and later to the vibratory screen in order to screen and classify to the requested particle sizes. Based on final product particle size,different types of crushers can be used as jaw crusher, hammer crusher and roller crusher. Eventually the lime with required fraction will be stored in the storage silos. Depending on Customer request, final product can be filled from storage silos to the open trucks, bulk carrier, big-bags etc.
Types of materials that would result ouf of the process:
1) Calcined lime is the material that we get after the calcination and the crushing to different fractions from 0-3 mm to 0-80 mm, any other fractions between is possible.
2) Grinded lime is a second type of product produced in lime plant. In order to produce this product, other grinding and classifing equipment are used. Also based on the request of the Customer, storage silos and different type of filling and packing equipment are used in order to deliver grinded lime to the final users.
3) The hydrated lime is another final product which can be produced on the plant supplied by Parget&Maerz. The hydrated lime is obtained as a result of the reaction during the mixing of calcined lime with water in „hydrator”. Feeding of the lime to the hydrator is done by dosing and weighing belt conveyor. After lime is hydrated it is fed for primary seperation and for the grinding. Separation is done by dynamic air separator and grinding is done by ball mill. After the grinding, hydrated lime is fed back to the seperator for reseparation to meet the required fraction. Eventually, hydrated lime is stored in the storage silos and filled or packed to bulk carrier, big bags, PP bags ets.
Parget Lime Production Factory’s Units
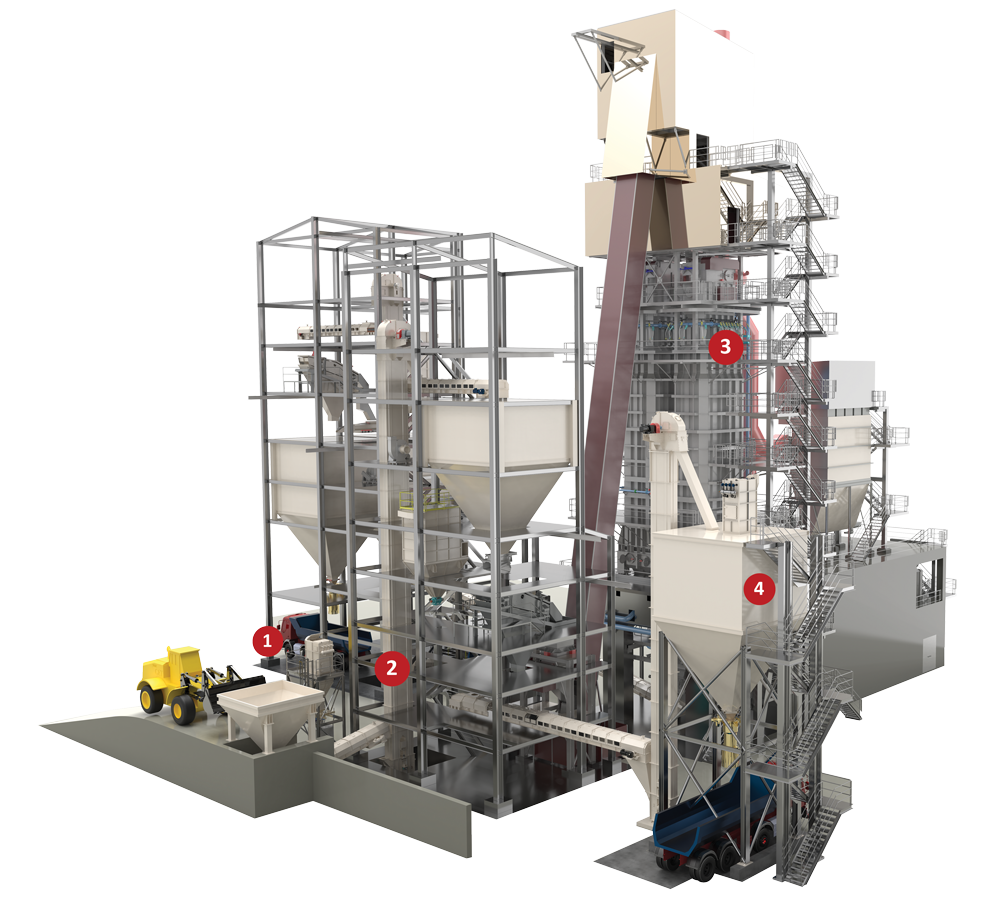
Raw material feeding unit
- Ease of maintenance.
- Smaller installed power, less electrical consumption.
- Possibility of using bucket elevator and belt conveyor for raw material feeding.
- Different desing based of quality of raw material.
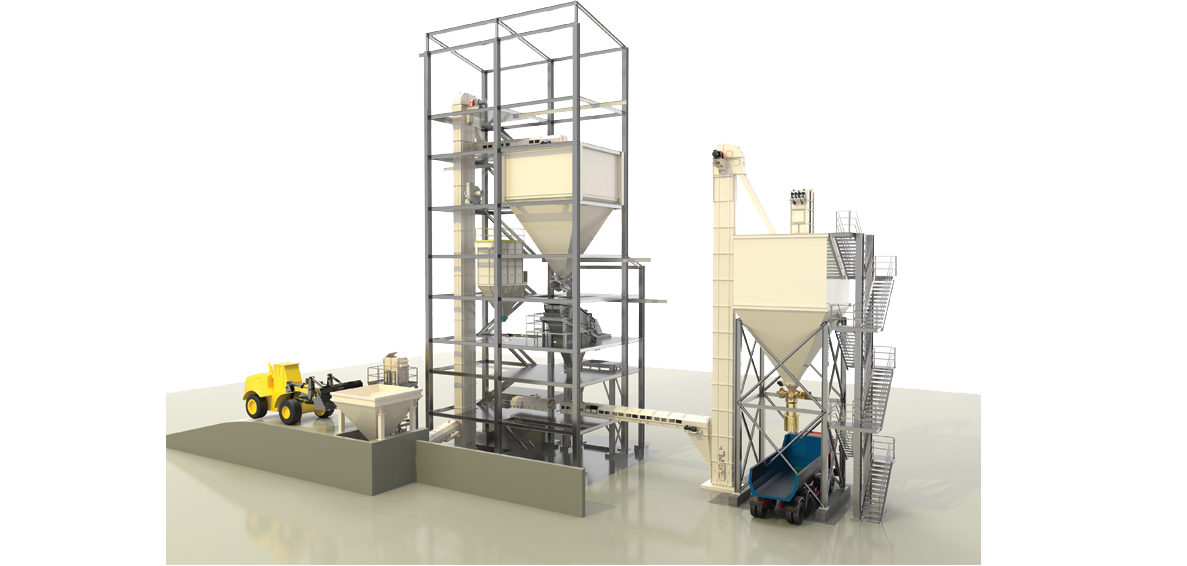
Raw material storage and screening unit
- Smartly designed unit and machineries according to the raw material quality tolerances.
- Smartly design of the unit in order to arrange uninterrupted operation of the vertical kiln
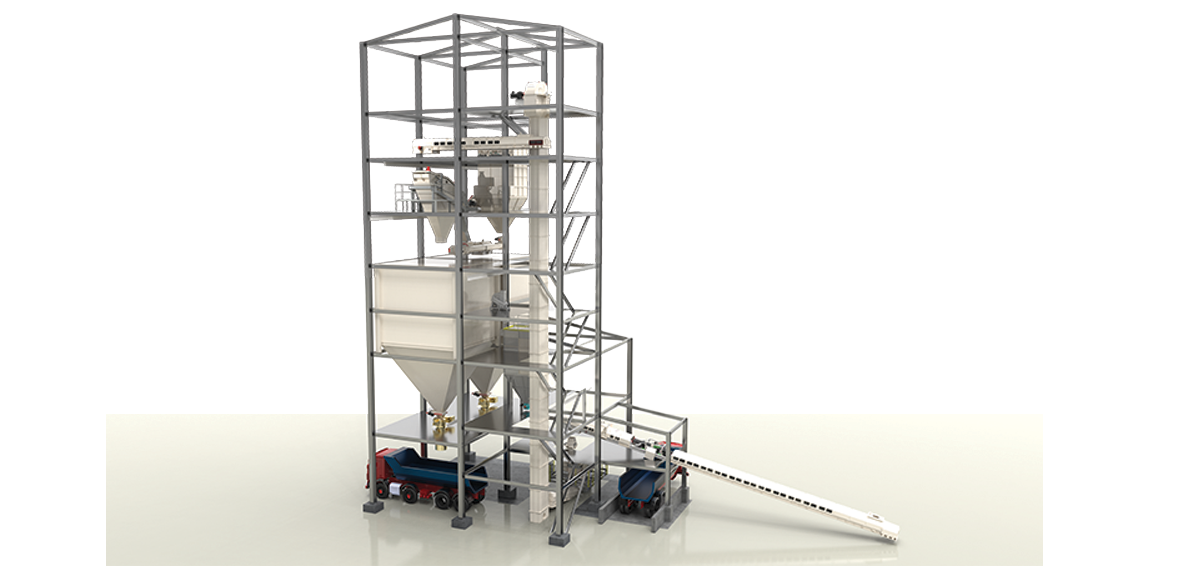
Calcination unit
- Using technology of years of experience and know-how by the best lime calcination technology supplier „Maerz”
- Smooth operation.
- Guaranteed product quality, less production losses.
- A lot of different types of fuel that can be used.
- Different types of kilns basing on raw material and final product quality.
- Completely automatic operation system
- Capacity ranges from 120 t/day till 800 t/day with one single kiln
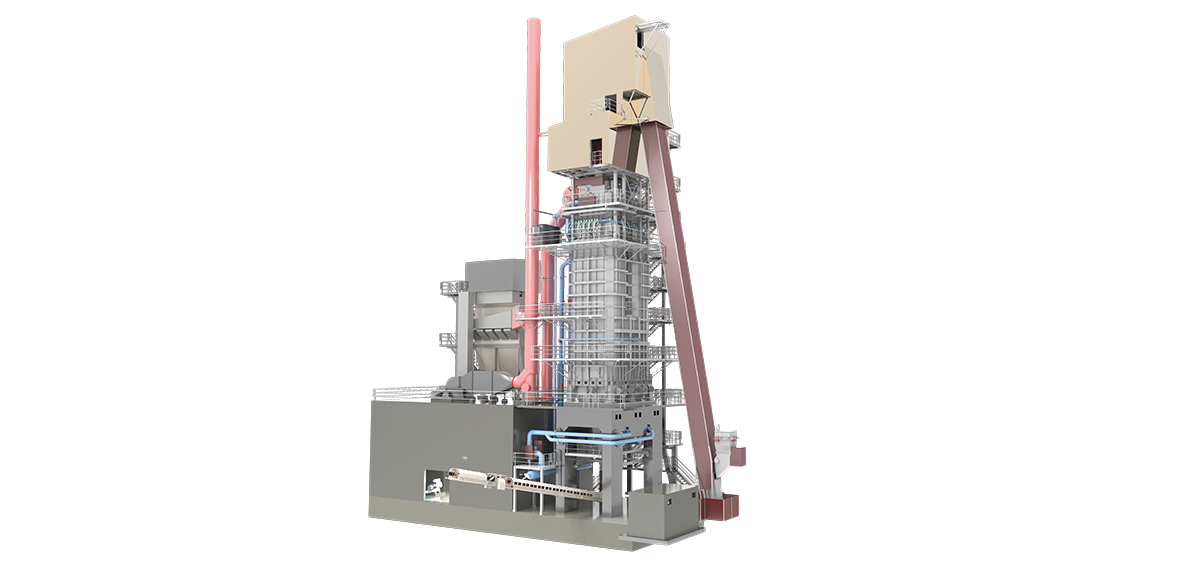
Lime handling, storage, crushing and filling unit
- Flexible design according to the requested material type and range.
- Different type of filling and packing possibilities.
- Compact design.
- Wide range of final product particle size.
- Possibility of production of quick lime or grinded lime.
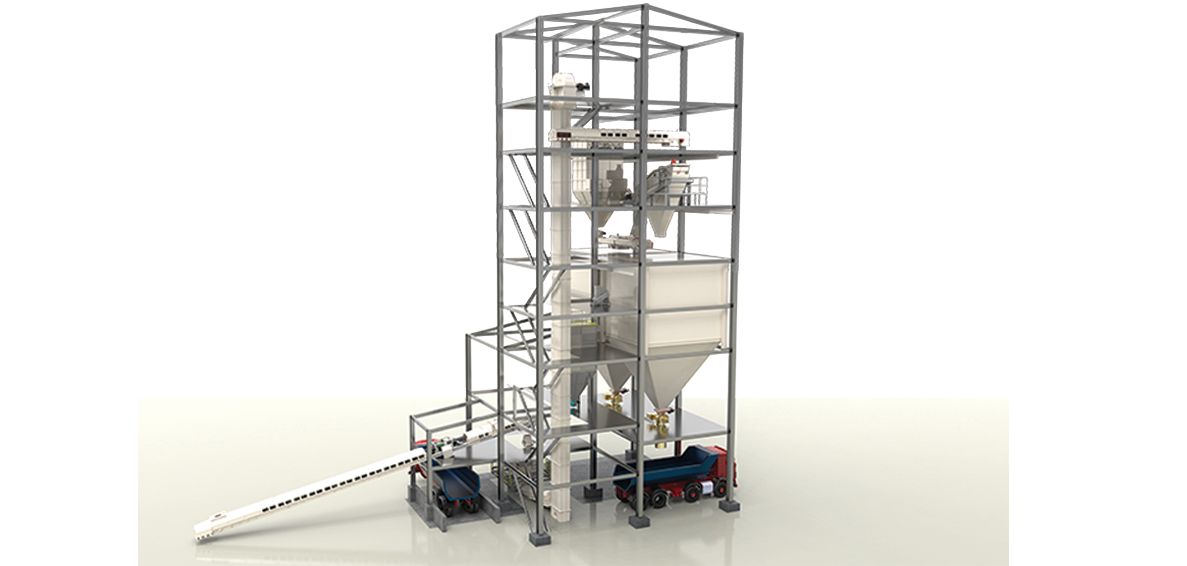
Hydration unit
- Maerz branded hydrator with best quality.
- Smart design of grinding and classifying systems.
- Guaranteed product quality.
- Possibility to produce different fractions with one single unit
- High level of automation for automatic operation and control
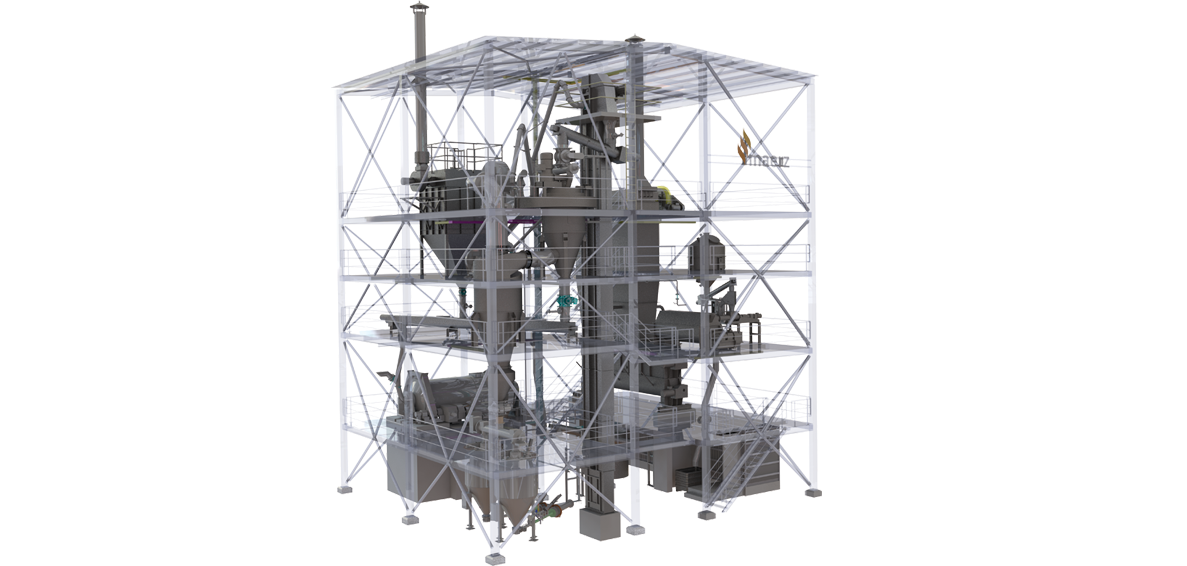